Agenda
- What is Stereolithography?
- SLA vs LCD (MSLA)
- Who is Stereolithography for?
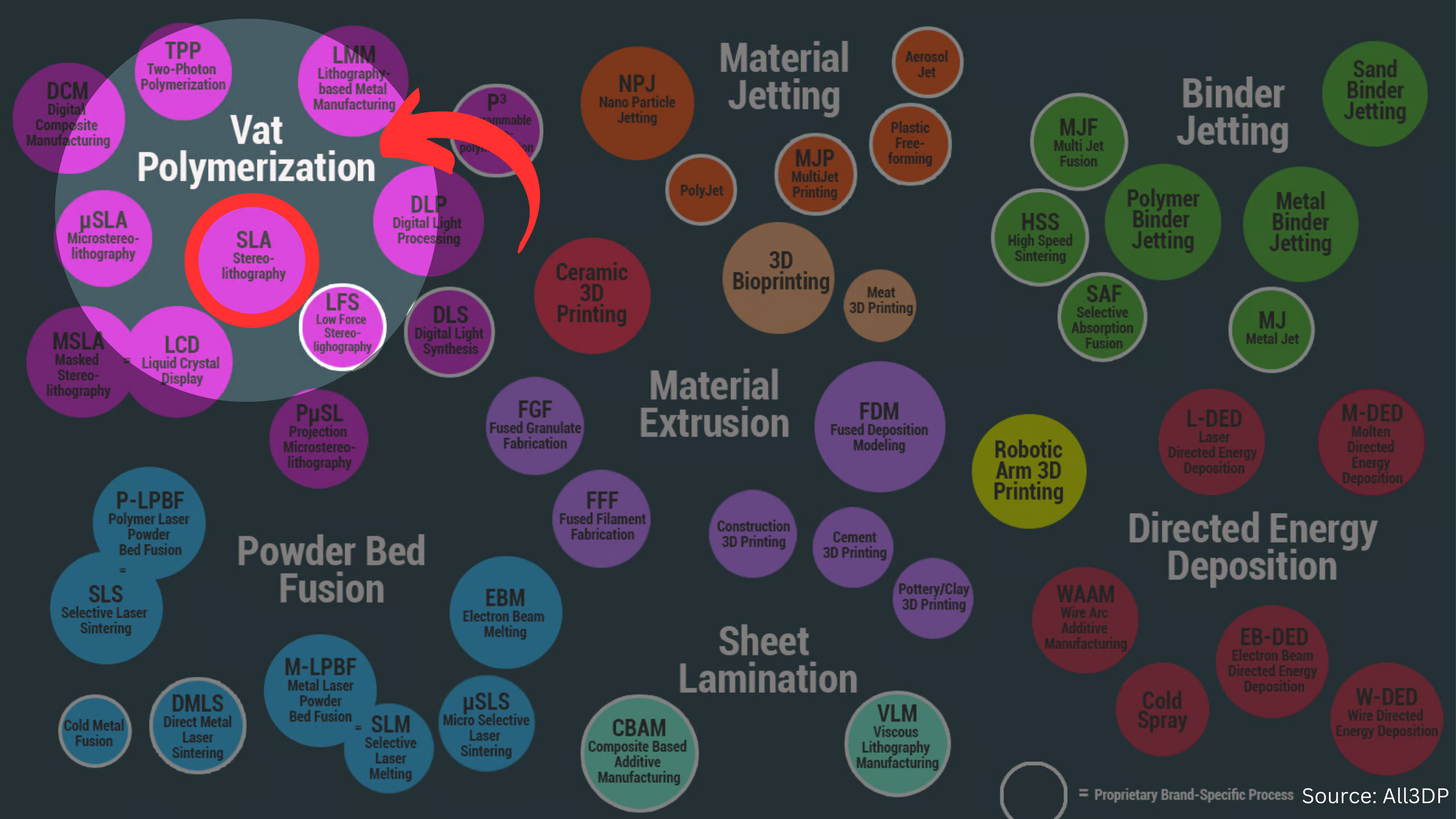
What is Stereolithography?
Stereolithography (SLA) is a 3D printing process that belongs to the "Vat Polymerization" family, it uses a UV laser to cure liquid resin into solid layers, building up a 3D object with high precision and smooth finishes. It is widely used for detailed prototypes, functional parts, and molds.
How does Stereolithography Work?
- Layering: A thin layer of liquid photopolymer resin is spread across the build platform.
- Curing: A UV laser selectively cures the resin, solidifying it according to the design.
- Layer-by-Layer: The build platform lowers slightly, and a new layer of resin is spread and cured, repeating the process to form the 3D object.
- Post-Processing: The printed part is removed, rinsed to remove excess resin, and post-cured under UV light for added strength and durability.
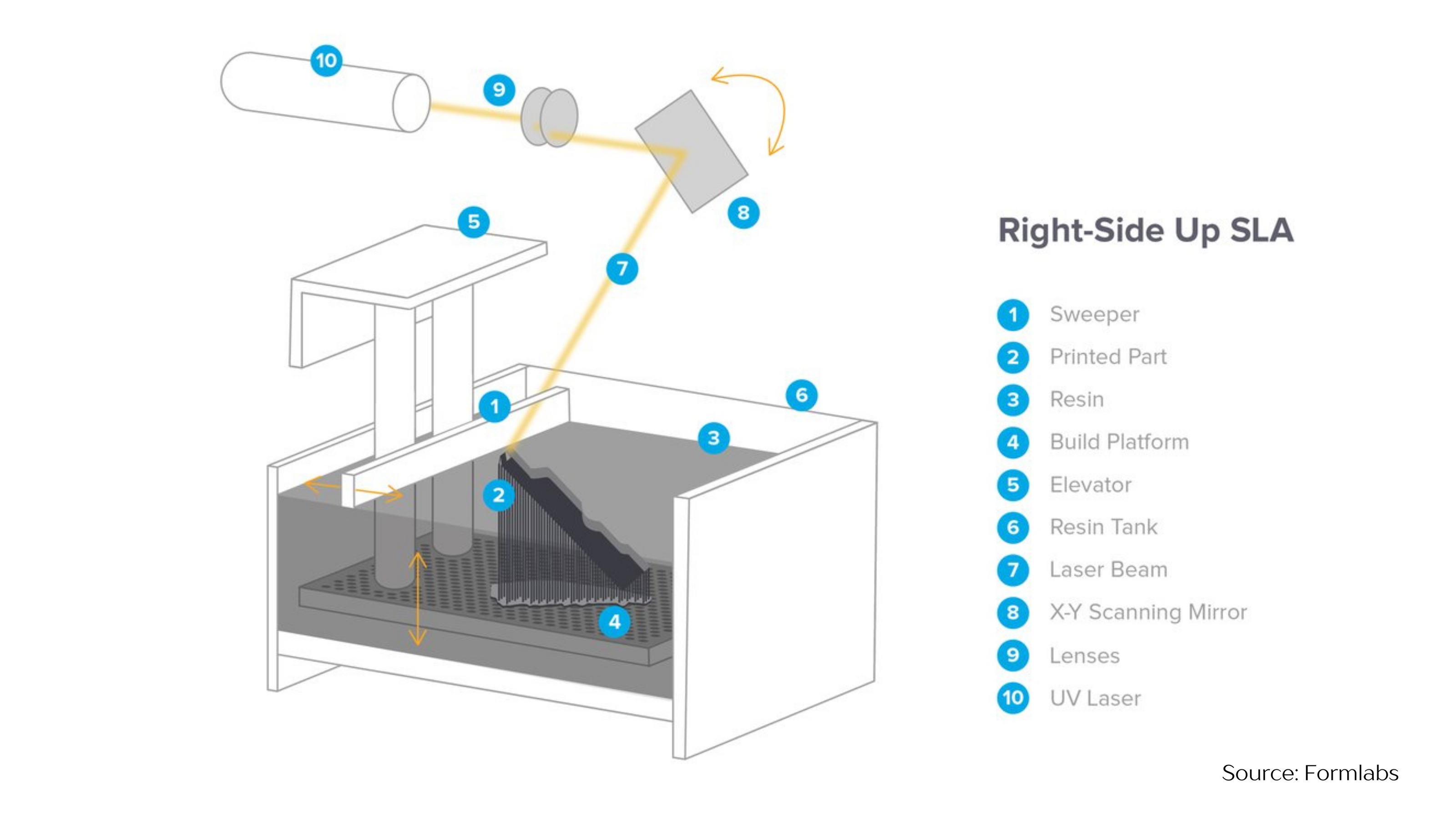
What is the difference between SLA and other Resin 3D Printing technologies?
Vat polymerization is a 3D printing process where a liquid photopolymer resin is selectively cured layer by layer using an Ultraviolet UV light source, such as a laser or a projector, to create a solid 3D object with fine details and smooth finishes.
SLA or Stereolithography is part of the Vat Polymerization family
Other Vat Polymerization technologies include:
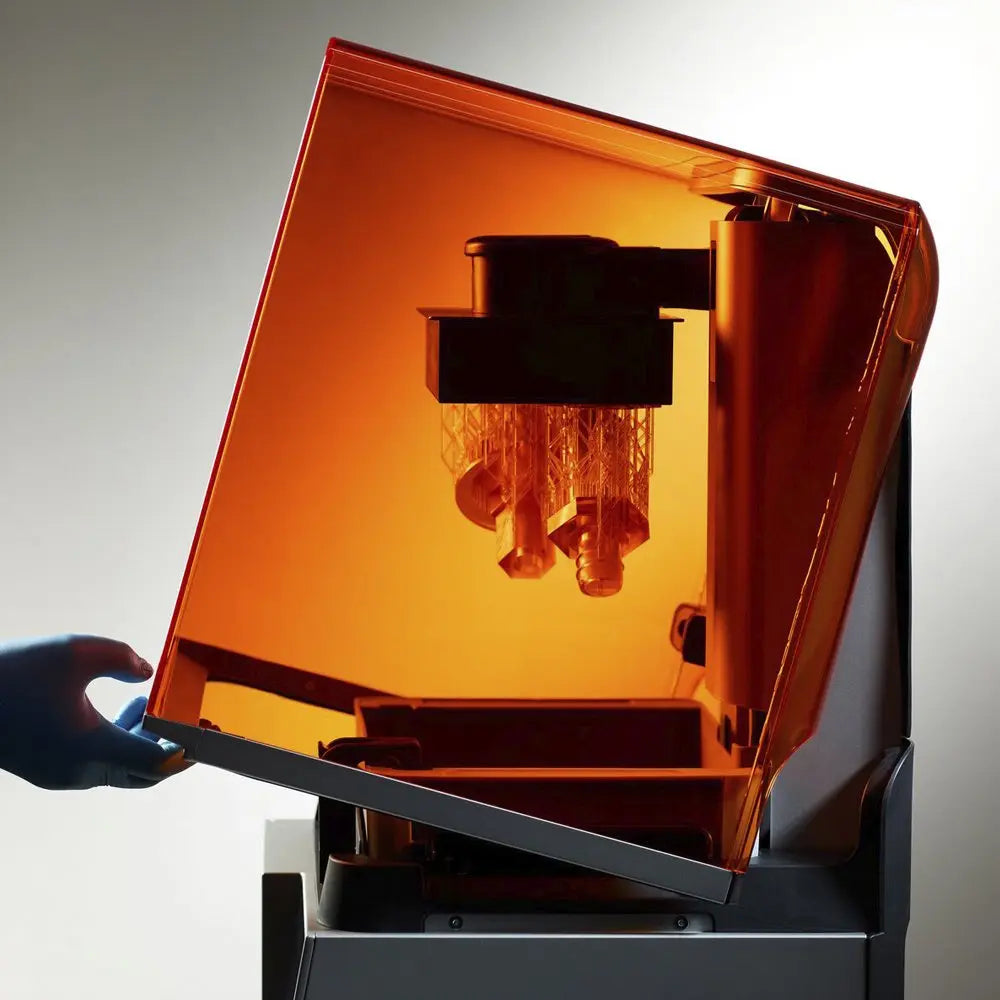
LCD / MSLA
Liquid Crystal Display
Or "Masked SLA", the more affordable, widely used, hobbyist level resin machines, employs an LCD screen as a mask to expose the resin layer by layer, offering cost-effective printing with good detail and resolution.
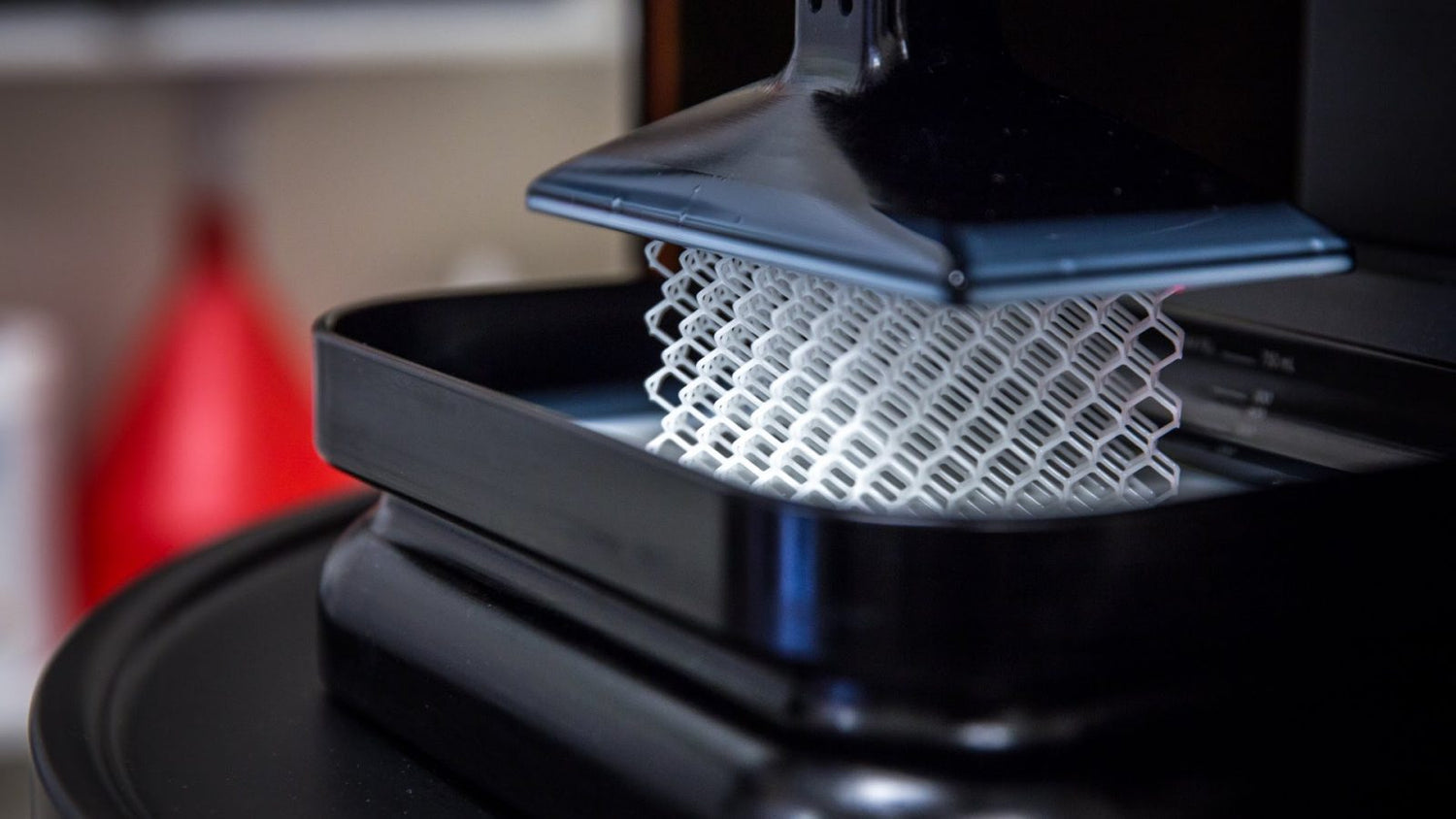
DLP
Digital Light Processing
Projects an entire layer of light using a digital micromirror device (DMD), curing the resin layer all at once, enabling faster prints compared to SLA.
Key Advantages of SLA over MSLA:
-
Higher Precision
SLA achieves higher accuracy due to its small, precise laser spot, unlike LCD's pixels that cause jagged edges
-
Higher Surface Quality
SLA produces parts with extremely smooth finishes, reducing the need for post-processing compared to LCD prints
-
Consistent Quality
SLA cures resin point-by-point, resulting in uniform part quality without visible layer artifacts caused by LCD's pixel grid
-
Large Print Volume
SLA printers, especially industrial ones, can have larger build areas without losing resolution, whereas LCD resolution is tied to screen size
-
LCD Screen Degradation
LCD screens degrade faster from UV exposure, causing reduced resolution and uneven curing. Lasers are more durable with proper use.
-
More Reliable Performance
Laser SLA systems are generally more robust and reliable, with fewer issues related to screen wear or uniformity
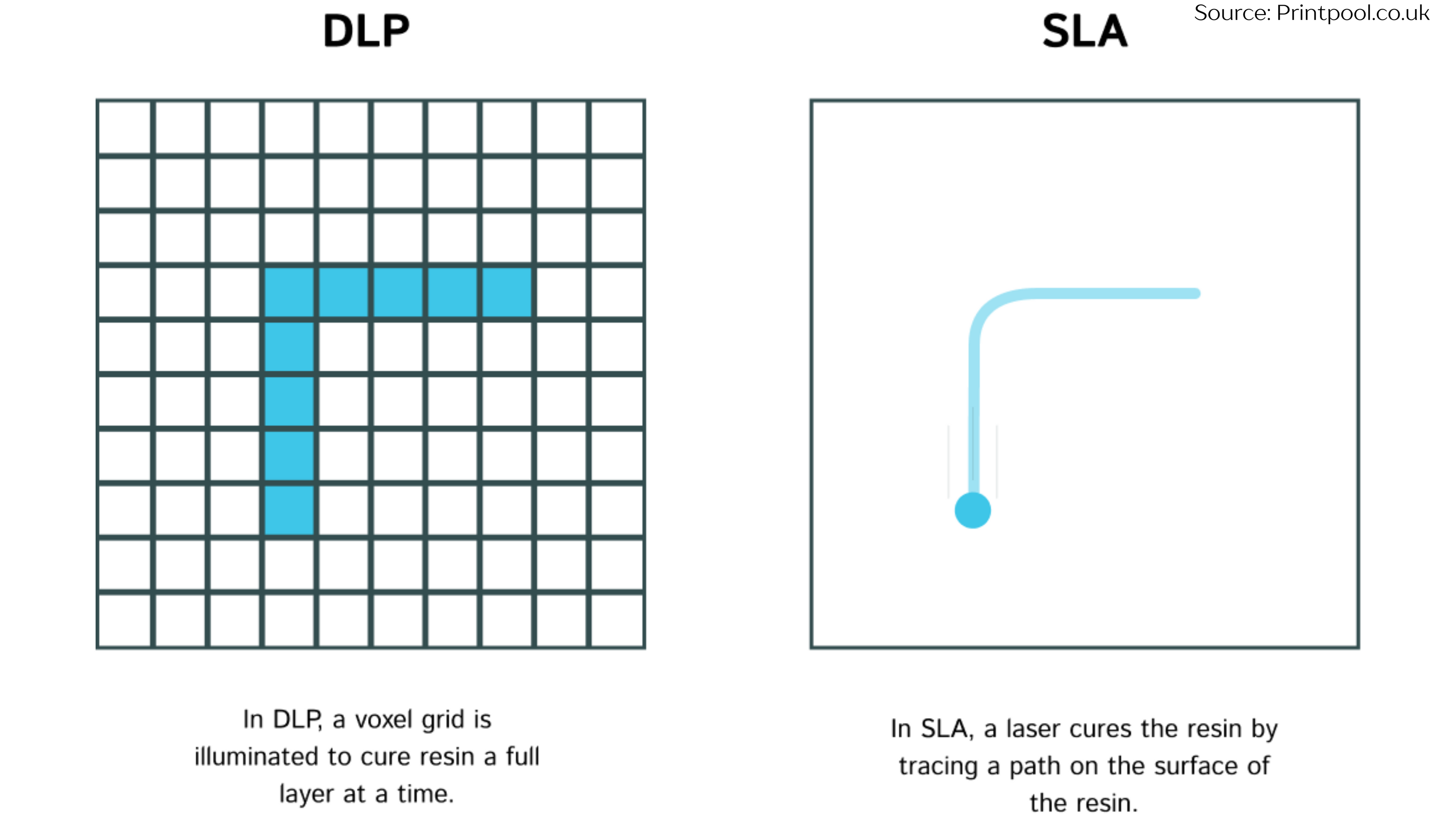
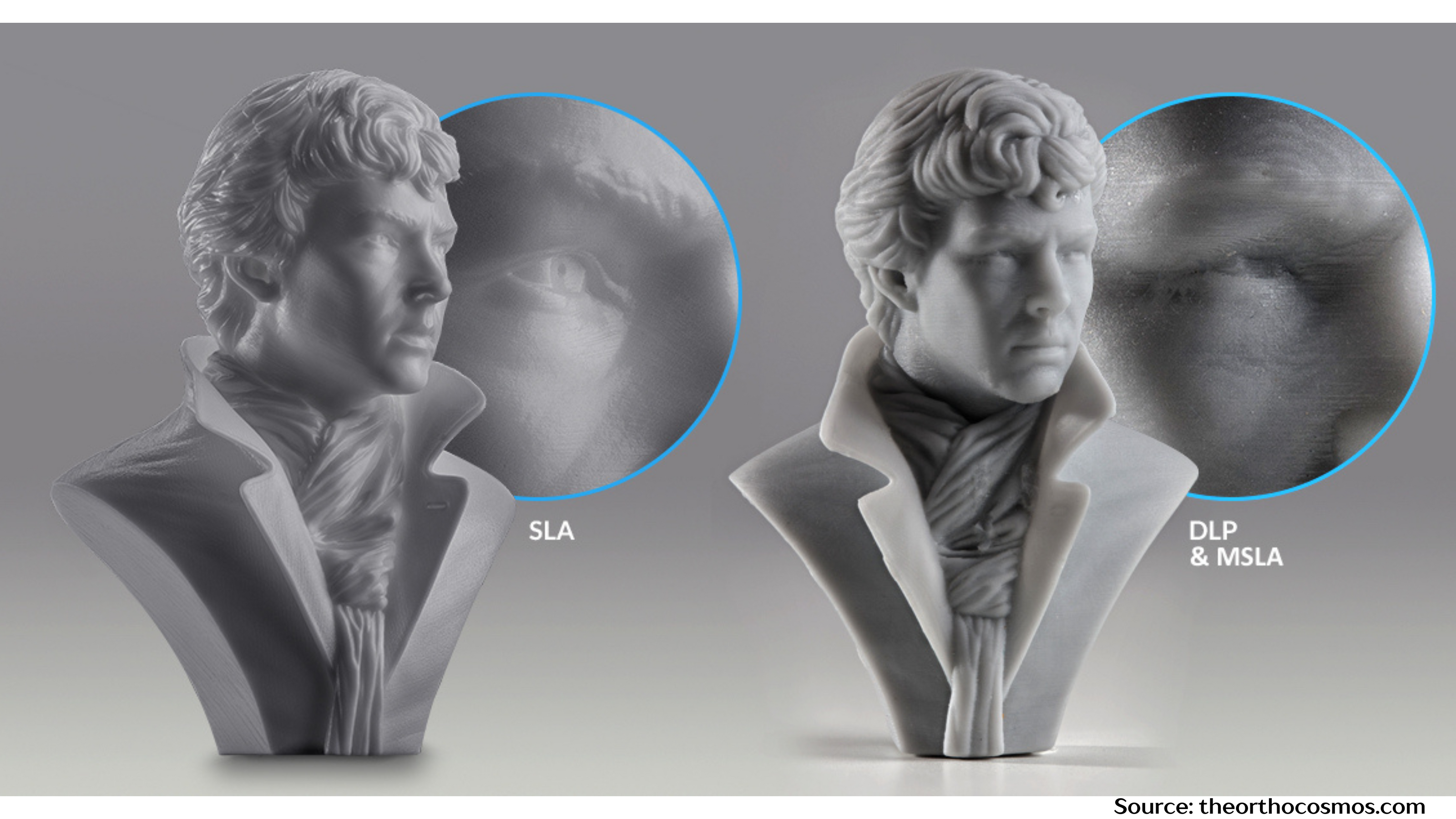
Who is SLA 3D Printing for?
-
Engineering & Rapid Prototyping
-
University & Education
-
Art & Design
-
Automotive & Aerospace
-
Medical, Dental & Jewelry
-
Architecture
Engineering: Rapid Prototyping

1. Functional Prototypes
SLA allows engineers to create prototypes that closely resemble final products in terms of detail, fit, and finish, enabling functional testing of designs before full-scale production
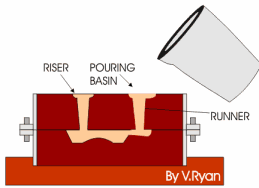
2. Complex Geometries
Engineers can design and print complex geometries, including intricate internal features, that are difficult or impossible to create with traditional manufacturing methods
3. Design Validation
SLA is used to produce parts for design validation, helping engineers check for form, fit, and function early in the development process.
4. Customized Components
Engineers can quickly prototype customized parts, tailored to specific needs or applications, such as brackets, enclosures, and connectors
5. Small-Batch Production
SLA enables cost-effective small-batch production for specialized components especially with the large print volumes the technology provides, reducing lead times and costs compared to traditional manufacturing
6. Tooling and Fixtures
SLA is used to create tooling, jigs, and fixtures for assembly or testing, providing precise, low-cost solutions for short production runs
Rapid Prototyping:
- Iteration and Testing
SLA enables rapid iteration of prototypes, with fast design-to-print cycles, allowing for quick testing and refinement of designs in real-world conditions. - Material Testing
Engineers can test different materials quickly to evaluate their properties, such as flexibility, heat resistance, and strength, helping to refine product designs. - Minimized Design Risk
SLA's ability to quickly produce functional prototypes helps reduce the risk of design flaws, ensuring better products at the end of the development cycle. - Low-Cost Prototyping
SLA offers a cost-effective solution for creating high-quality prototypes without the expense of tooling and molds, making it ideal for small businesses and startups. - Rapid Feedback Loops
Engineers can receive rapid feedback from stakeholders, testers, or customers on prototypes, enabling faster decision-making and product refinement.
Water Pump Casing Mold and Core (Source: Aniwaa)
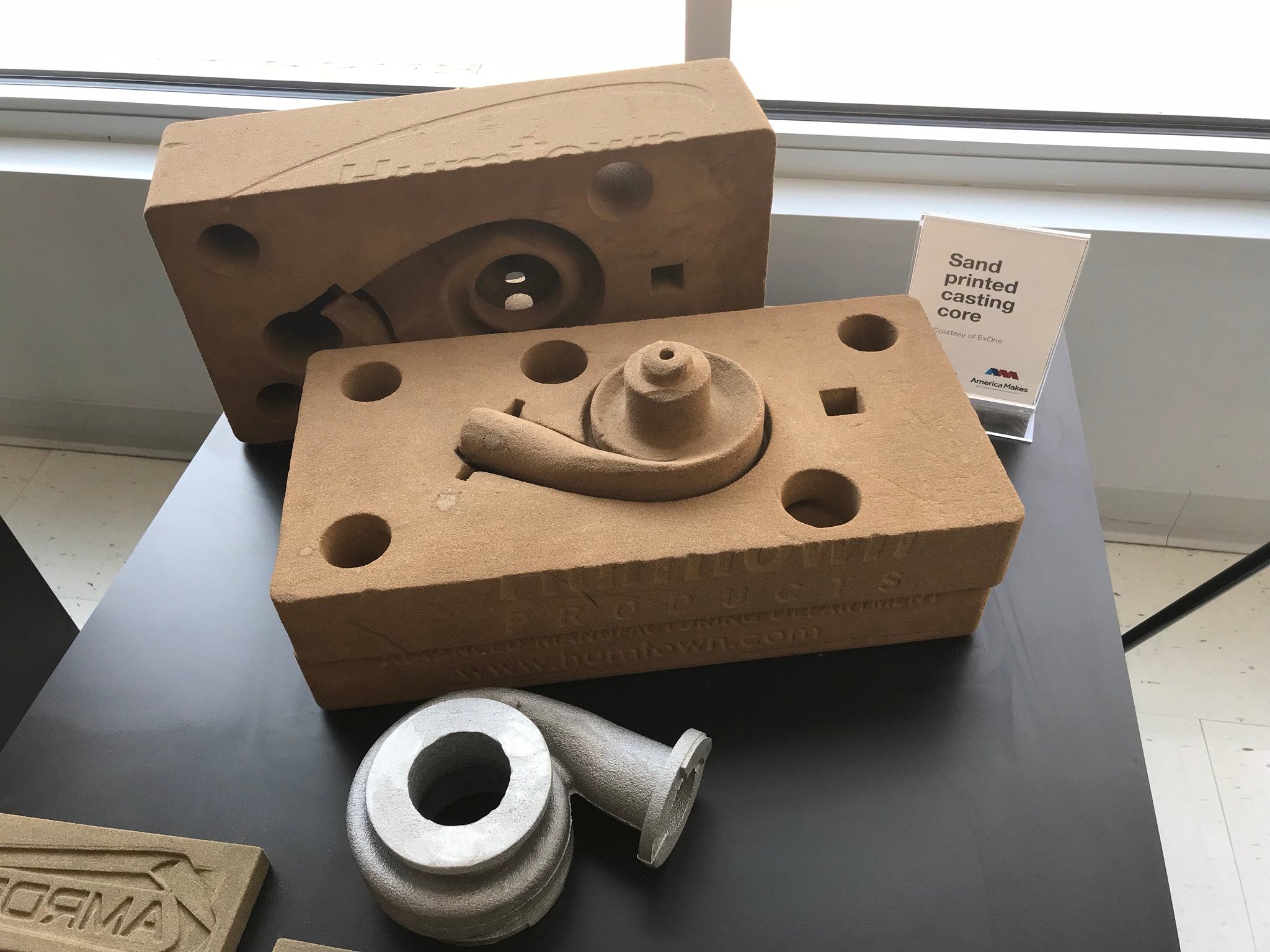
OK Foundry in Virginia uses a 3D printed sand mold to case a 1912 Velie engine block (Source: All3DP)
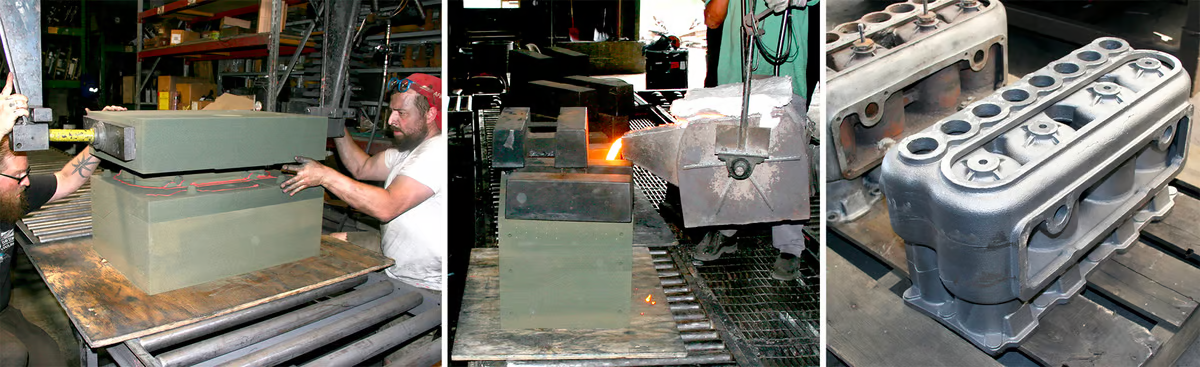
Sand Mold Vs. Final Steel Casted Part (Source: precious3d.com)
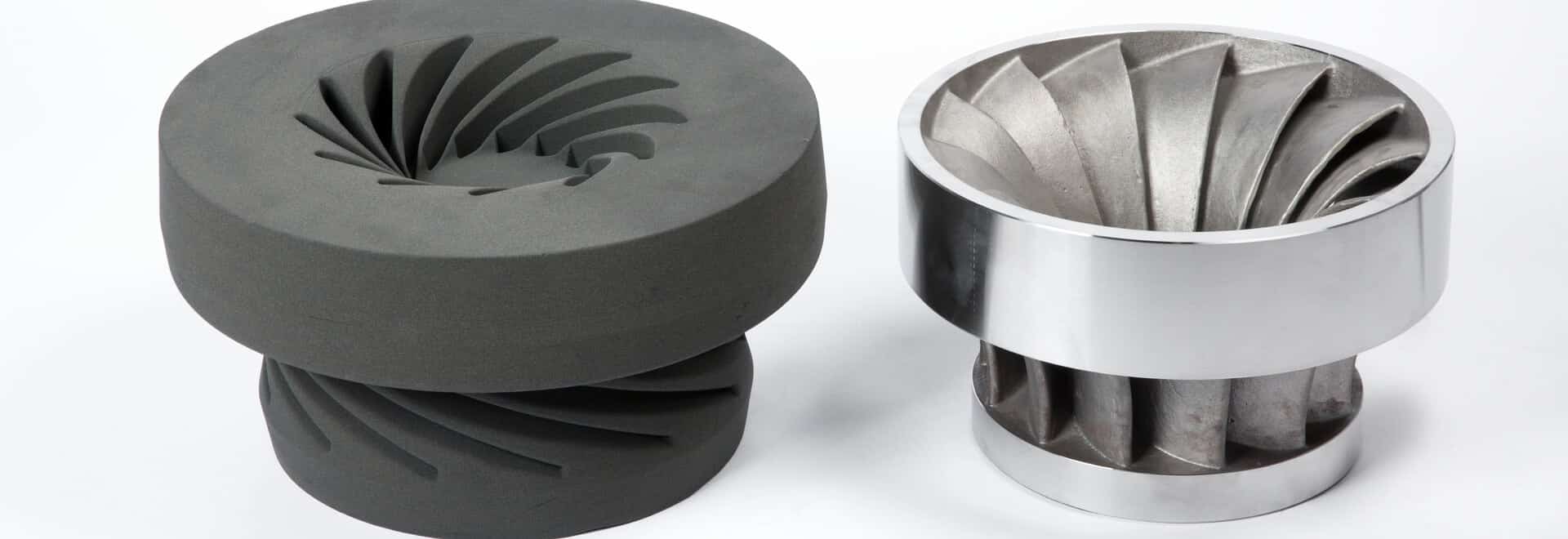
Universities & Laboratories
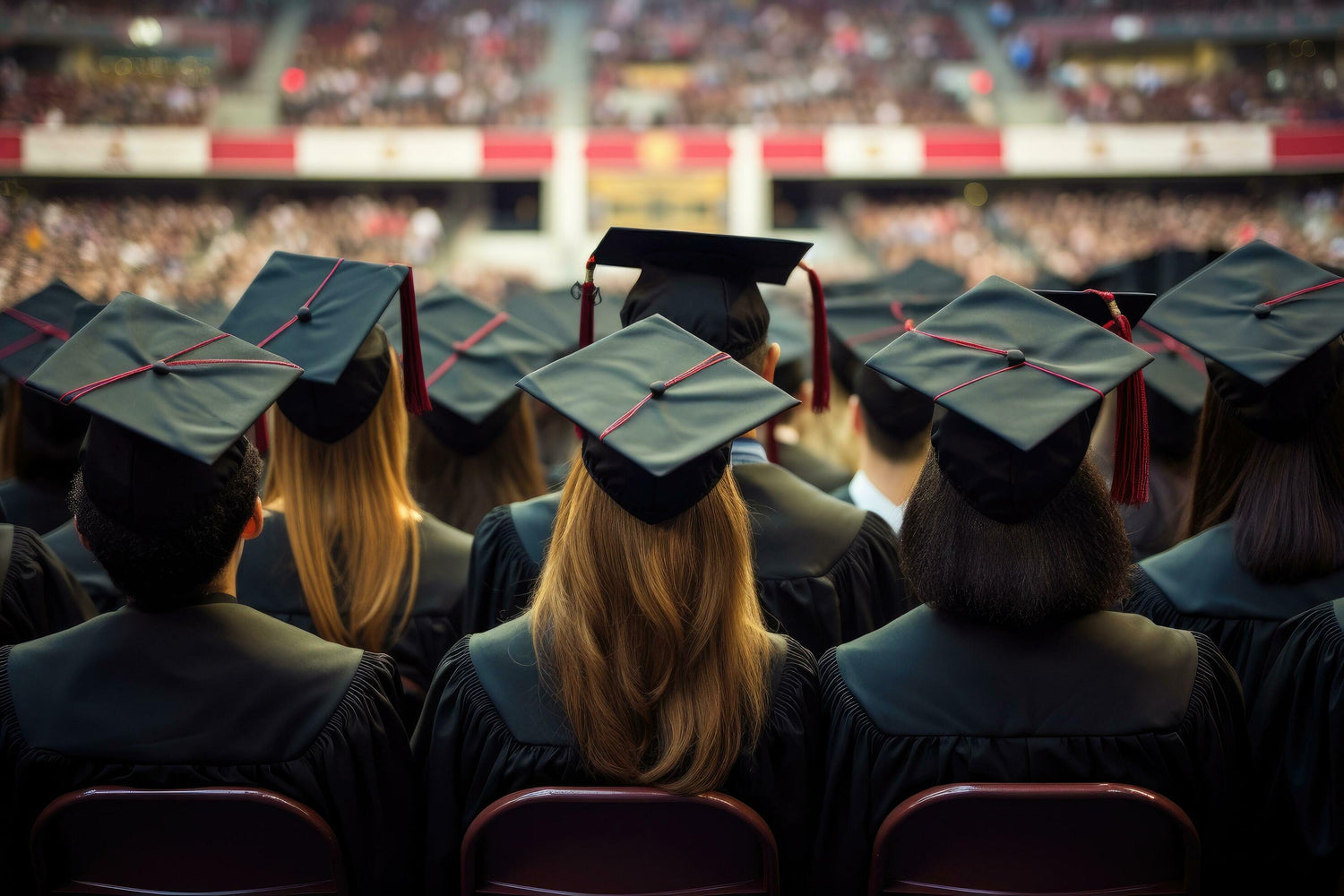
Sand 3D Printing can be utilized in educational institutions, particularly in engineering and manufacturing programs, for a variety of purposes

Teaching Advanced Manufacturing Technologies
Understanding Binder Jetting Technology: Students learn the principles and mechanisms behind binder jetting, including material compatibility, layering processes, and curing methods.
Digital Design and Prototyping: Using CAD software, students can design complex parts or sand molds and print them to see how their designs translate into physical objects.
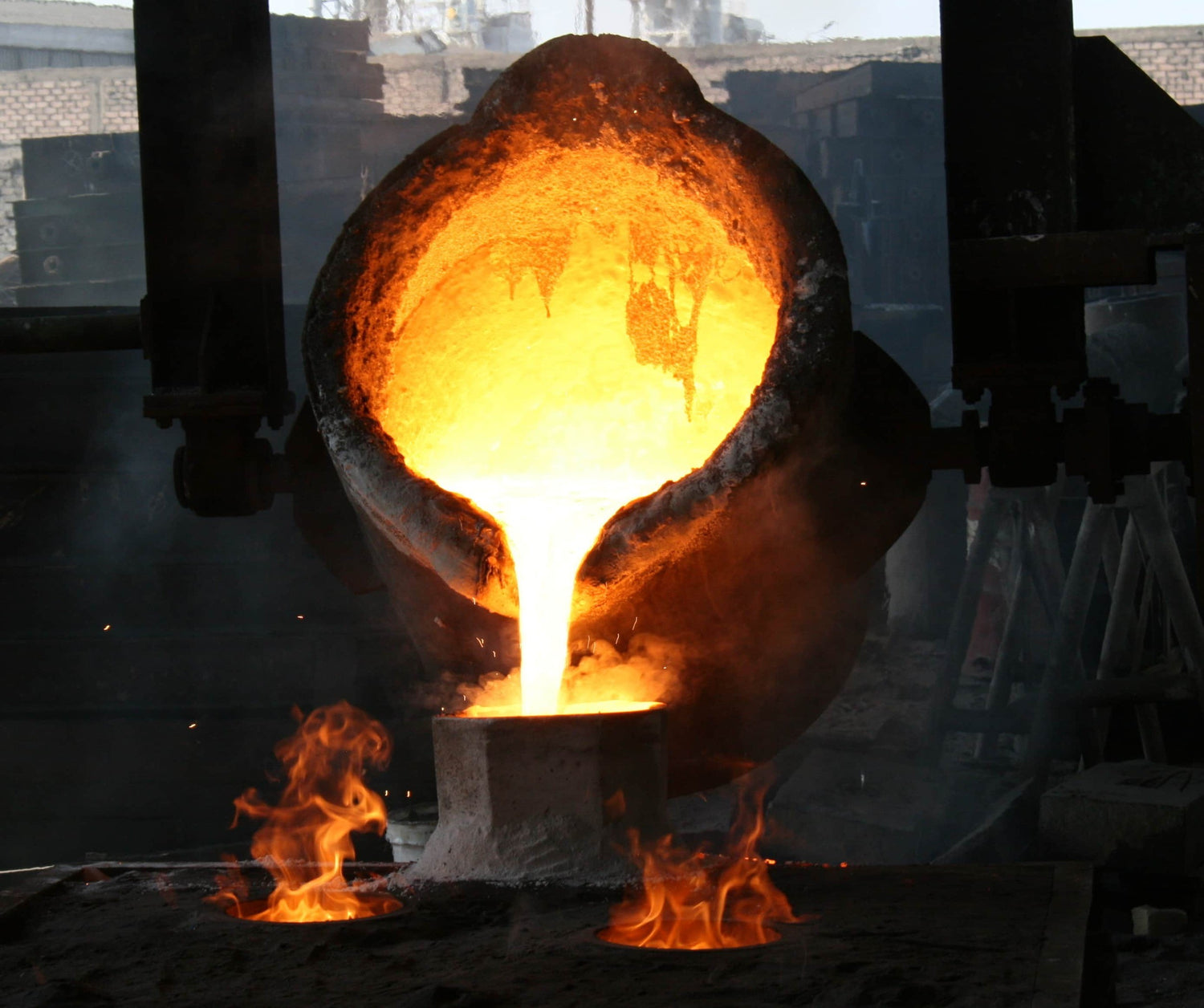
Casting and Foundry Training
Producing Sand Molds: The machine allows students to create precise sand molds for metal casting, enabling hands-on experience in the foundry process.
Experimenting with Materials: Students can test different types of sand, resin binders, and curing methods to understand how material properties affect casting outcomes.
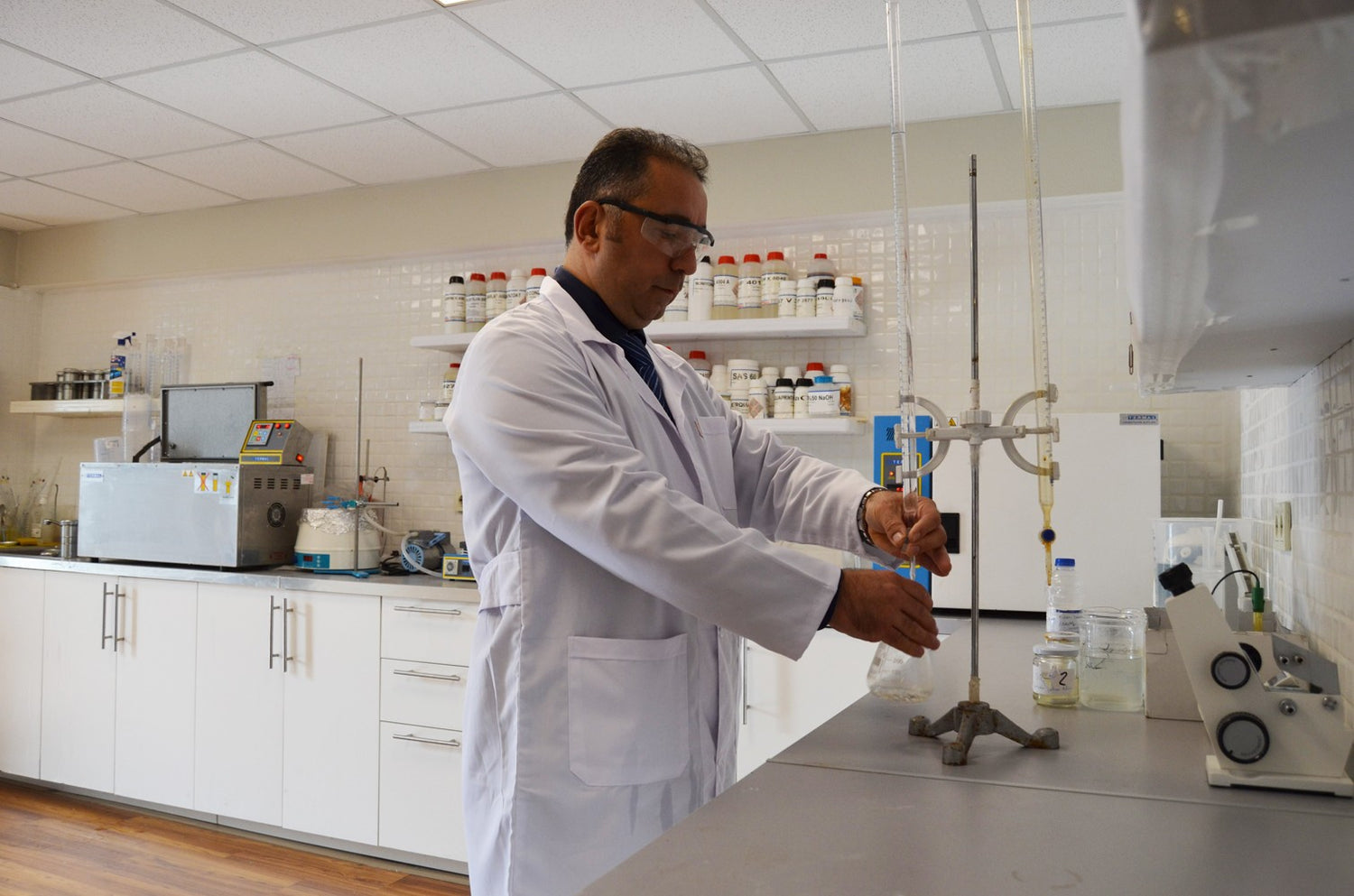
Research and Development
Innovating Casting Techniques: Universities use the machine to explore innovative methods for producing molds and cores, such as integrating cooling channels or complex geometries.
Studying Material Behavior: Researching how different sand compositions and binder formulas perform in industrial applications.
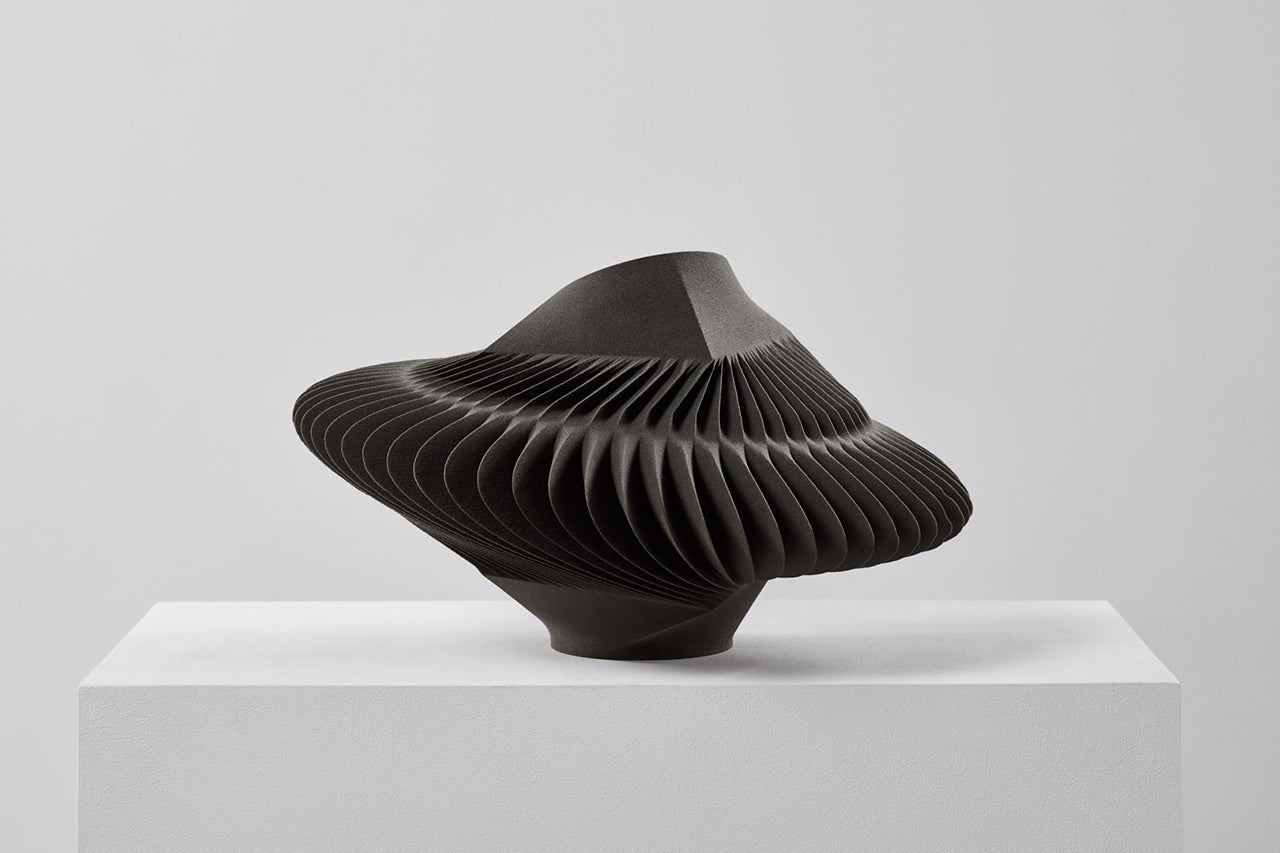
Interdisciplinary Applications
Art and Design: Students in design programs can use the machine to create intricate sand molds for artistic metal casting projects.
Mechanical and Civil Engineering: The machine can be used to teach structural principles by creating and testing custom shapes or components.